一、定義階段
1、確認顧客需求和過程根據CS部門(客戶服務)的數據反饋,目前TV主板撞件不良的顧客抱怨高達70%。
根據調查可知,從該公司4月的分析修理品質數據看,TV主板撞件不良居于TOP 1不良,占總不良74%,故選擇主板撞件不良進行改善。
撞件不良是主板制程過程中的主要不良,發生撞件則需要進行返工、維修,影響產線效率,提高生產成本;更為嚴重的是,如果撞件的點位機器(ICT/FT)無法檢測出,極易導致不良漏失到市場,從而顧客抱怨,給產品的品質和公司的聲譽造成很大的影響。
對TV主板撞件進行SIPOC分析,定義改善項目的過程。
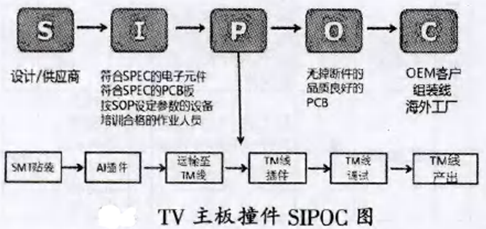
2、確定項目計劃與項目團隊
在完成以上工作后,要保證項目的有效推行,就必須制定項目進度計劃。
定義階段:2012.4.15-2012.4.30,主要定義項目,組成項目團隊,明確改進目標。
測量階段:2012.5.1-2012.5.15,主要測量主板撞件的趨勢及主板生產流程現狀。
分析階段:2012.5.16-2012.5.30,主要分析流程現狀,找出導致撞件的關鍵因子。
改善階段:2012.6.1-2012.6.30,主要是針對關鍵因子提出改善方案。
控制階段:2012.7.1-2012.7.30,主要是對改善成果進行標準化、規范化。
要保證改善項目的推行,良好的項目團隊必不可少,這是保證六西格瑪項目取得成效的一個重要因素,根據公司的實際情況及TV主板的生產過程,TV主板品質改善的項目小組結構如下:總Team Leader: IE經理,負責下達工作任務和目標。
Team Leader: PCBA部門主管,主導專案的推動與執行。
黑帶大師:由該公司六西格瑪部門協理擔任,輔助解決專案推行中的難題。
FL:治具課負責設備改造、泳焊治具制作修整。
IE:負責數據收集整理、項目分析推行、標準工時評估,負責錫爐參數調整及PCB板LAY-OUT修改,并追蹤各制程改善情況。
PD:負責M線制程標準的執行,及M線制程的追蹤和不良數據的搜集,配合IE工作。
AI:負責A/I制程標準的執行,以及A/I制程的追蹤和不良數據的搜集。
SMT;負責SMT制程標準的執行,以及SMT制程的追蹤和不良數據的搜集。
QC:負責稽核TM線/AI/SMT各階動作標準化執行狀況。發布稽核報告:RD:負責標準化零件,優化PCB板layout設計。
3、確定項目度量指標
根據當前TV主板撞件不良狀況,根據制造處的KPI設定,需在7月份將TV主板撞件不良率下降至700PPM。
分析修理不良率(PPM) =ICT/FT擋下的不良板數/產出總量
二、測量階段
1、TV主板撞件不良趨勢
首先收集該公司TV主板撞件不良的數據,了解主板撞件的目前狀況。
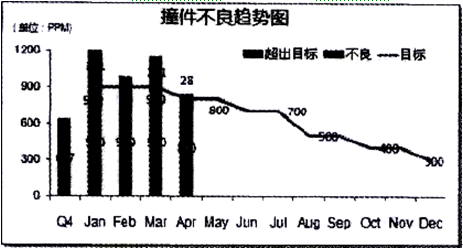
從數據中可以看出,TV撞件不良超過設定的目標值,急需進行改善。
在SIPOC圖宏觀把握流程的基礎上,利用細部流程圖,找出所有微觀流程對應的變量輸入和輸出,并選定可控制的、影響關鍵質量特性的因子,做后續的篩選和深度分析。TV主板制程的細部流程圖如下:
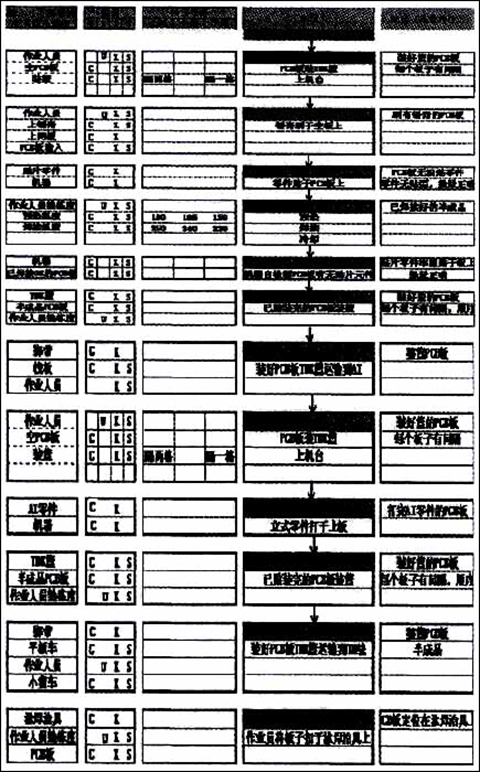
三、分析階段
分析階段采用FMEA分析,對各階別制程中關鍵輸入輸出進行失效模式分析,找出RPN值較高的失效因子,以找出導致撞件不良的潛在根源原因,通過FMEA分析可以得出導致撞件的主要失效因子是:SMT印刷機、AIS收板裝籃、運輸、TM線投板上治具。


通過FMEA分析可以得出導致撞件的主要失效因子是:SMT印刷機、AIS收板裝籃、運輸、TM線投板上治具。
四、改善階段
針對主要失效因子,采用頭腦風暴法,制定的撞件不良的改善對策如下:
1、SMT印刷機操作改善
針對PCB上板印刷時支撐PIN頂到下板,導致下板零件破損的問題,首先將此不良做成案例,對維修人員進行培訓;同時產線主管宣導所有人員支撐PIN位置有變動后,必須使用對應支撐PIN治具進行再次確認,確保不會頂到下板零件,并且后續每個月針對支撐PIN的規范及注意事項做一次宣導;此外,支撐PIN必須用實物板治具調節,所有線別均需配備實物板治具。
2、制定AIS收裝籃動作規范
①作業人員裝板時必須按從下到上的順序,由QC持續稽核作業人員作業。
②全員宣導,操作員裝籃時,應嚴格按照SOP作業(板與板的間隙為兩隔)。杜絕相鄰兩塊板發生碰撞;此外,采用防呆法,防止作業人員看錯格,每隔2格處對籃筐進行彩色標示,表示此格放板。
③規范投板站作業動作,一次只能取一片板子,由QC/PD/IE聯合稽核。
④針對兩排裝板,易疊板導致板邊零件撞件,標準化TKD籃,取消綁帶,增加檔桿避免疊板。
⑤定期檢查周轉車及TDK籃,確保周轉車的每個旋鈕沒有滑牙,松動,檢查每一輛周轉車的擋桿,無擋桿周轉車不能進行使用,需要及時更換;確保籃框無因變形。
(6)運輸統一采用標準化的周轉車,防止大尺寸PCB超過籃筐,標準化后的周轉車無需外側綁綁帶。
3、制定運輸改善對策
①運輸作業人員須依據拉板SOP作業,并檢驗周轉車是否符合要求,嚴格遵守規范。
②運輸作業人員每次只能拉一輛周轉車或一棧板TDK籃。
③運輸過程中,避免與障礙物或其他周轉車碰撞。如不小心碰撞應及時告知相應責任主管。
④進出電梯時若發現電梯與地面存在較大高度差,不得強行進入,避免劇烈震動造成塌框不良(應重新升降電梯或換乘其他電梯,并告知領班通知工程部維修)。
⑤在舊廠和北廠運輸的板子,裝載工具進出貨車時需放好僑聯鐵板,避免劇烈震動或車輪卡住。
⑥在運輸過程中,有發現塌框現場需要第一時間告知主管,并在原地進行處理。塌框板須重新檢測。
4、TM線改善對策
①針對投泳焊治具站位,投放泳焊治具時,嚴禁作業員在軌道上甩放治具,造成治具嚴重碰撞,并需對泳焊治具進行檢查,及時清理泳焊治具上的錫珠錫渣,應準備相應的清理工具。
②針對分板站位,制定的改善對策如下:
1)作業員上班前需對分板機進行點檢并填寫點檢List,預防機臺異常造成撞件。
2)分板時要平行切板,PCB放入導軌時需平放,不可左、右、上、下傾斜。
3)不允許采用手掰板方式進行分板,如分板機無法將板分斷,馬上聯系IE與FL。
4)PCB板需放置在防靜電片上,且不可出現疊板現象。
5)取板時,輕拿輕放,從上往下取板,一次一片,且要平行抽取,作業時手背朝下。
6)異常板子應暫放在TDK籃內,或放保麗龍上。
7)投板時,要將板子對準治具到位后,輕輕放入治具內。
五、管控階段
1、IE制定相關作業標準(防斷件掉件作業注意事項),并列入SOP指導作業,并制定相應的培訓教材,各部門安排專人對作業員進行培訓及考核,產線執行標準化動作,TM線/AI/SMT各階執行狀況,發布稽核報告,后續新進員工培訓并考核后再上崗,并且每月對新老員工進行培訓考核。
2、實施多部門聯合稽核。撞件不良是由不規范作業及部分改善對策及預防措施執行不夠徹底而造成的品質隱患。因此成立稽核小組,多部門定期、不定期對生產過程中人員作業方式進行稽核,對作業不良者重新培訓,如作業者多次出現錯誤,則吊銷上崗證,以規范作業員動作,從源頭上預防撞斷件不良的發生。
3、建立制程應力點檢制度。為了防止零件由于PCB發生應變造成斷裂,凡是存在應變之站位及場所,主要針對PCBA的組裝全過程(如AI自動插件、運輸、MI、分板、ICT/FT測試、插PIN、鎖付、組裝等)每2周進行一次應變測試管控。
再采取一系列改善管理的措施后,收集SFIS的數據了解撞件不良率。