光纖快速連接器質量改進過程
1、定義階段
在DMAIC定義階段,需定義項目的選題依據(jù)、改進機會、改進目標、項目計劃和項目組成員等。
項目依據(jù):該公司在光纖快速連接器的兩周試生產中,總共生產了10689個產品,其中有1702件產品報廢,報廢率為15.9%,一次通過率只有49.8%。
改進機會:當前的生產一次通過率太低,報廢率太高,浪費了大量的人力物力。
項目組成員:由生產部、研發(fā)部、工藝部、質量部、設備部以及財務部共派出成員組成。
改進目標:通過六西格瑪DMAIC改進方法的實施,改進缺陷,使產品報廢率降低到7%以下,一次通過率提升至80%以上。
2、測量階段
將兩周的試生產缺陷記錄進行柏拉圖分析,得出端面不良、干涉儀測試不過、光學測試不過為主要缺陷,占了不合格總數(shù)的90.3%,這三個流程都是測試和檢測環(huán)節(jié)。因此先進行測量系統(tǒng)分析,正確的測量永遠是質量改進的第一步。
干涉儀是干涉儀測試中會用到的主要設備,需要測試光纖快速連接器的光纖高度、頂點偏移、曲率半徑和APC角度,這些測試項都需要進行測量系統(tǒng)分析。工程技術人員選取10個樣本,3名檢驗員進行檢驗,每位檢驗員對每個樣本重復檢驗3次,并將測試數(shù)據(jù)輸入Minitab軟件,進行Gage R&R分析,得出了干涉儀測量系統(tǒng)的曲率半徑、頂點偏移、光纖高度以及APC角度的測量系統(tǒng)能力分別為8.29%、5.14%、6.89%和3.04%,這些值均小于10%,因此干涉儀測量系統(tǒng)滿足測量系統(tǒng)要求。
端面檢測是檢測員用400倍的顯微鏡觀察研磨后的光纖快速連接器的端面,根據(jù)看到的端面的劃痕、凹點及凹陷和裂紋的多少和大小來判斷端面質量是否符合要求。由于端面質量主要由檢測員通過目視進行檢測,該測量系統(tǒng)屬于屬性值測量系統(tǒng)。工程技術人員選取55個樣本,由2名檢測人員進行檢測,每名檢測人員對4個樣本重復檢測2次。樣本既包括合格品,不合格品;既包括明顯不合格品或合格品,又包括介于合格與不合格之間的產品,即樣本涵蓋了整個生產過程的產品范圍。將測試數(shù)據(jù)輸入Minitab軟件,進行屬性值Gage R&R分析,分析結果如表1所示。
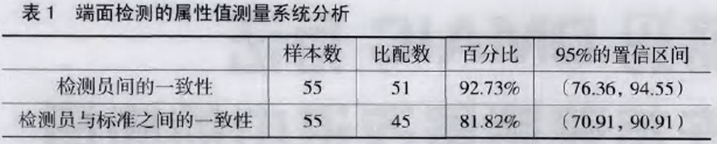
從表1可以看出,測量系統(tǒng)的匹配百分比為81.82%,達到了測量要求。
光學測試是測試員將成品光纖快速連接器插入光學測試儀,然后讀取測試儀輸出的插入損耗和回波損耗,測試結果完全取決于光學測試儀,而光學測試儀在每次使用前都會進行校準的,因此是可信的。
3、分析階段
結合前面階段得知的造成成品率不高的3個主要缺陷,通過仔細研究光纖連接器的生產流程和操作手冊,發(fā)現(xiàn)干涉儀檢測和端面檢測都是對研磨工序的檢測,而測量系統(tǒng)是可信的,因此,研磨工位的質量缺陷應該是造成整個光纖連接器成品率不高的最主要原因。
研磨是指使用端面研磨機對光纖快速連接器端面進行打磨和拋光的一道工序,用端面研磨機對光纖端面打磨和拋光的過程有4個步驟,涉及D30um、D9um、D1um和SONG4種型號的研磨片。研磨出的端面的質量幾乎決定了光纖連接器的性能,因此研磨環(huán)節(jié)是光纖快速連接器生產過程中最精密也是最核心的步驟。但是在實際生產中研磨工位影響因素眾多,而且各因素并不完全獨立,因此項目組決定采用頭腦風暴法,并繪制因果圖對人、機、料、法、環(huán)各因素進行逐一分析,如圖1所示。
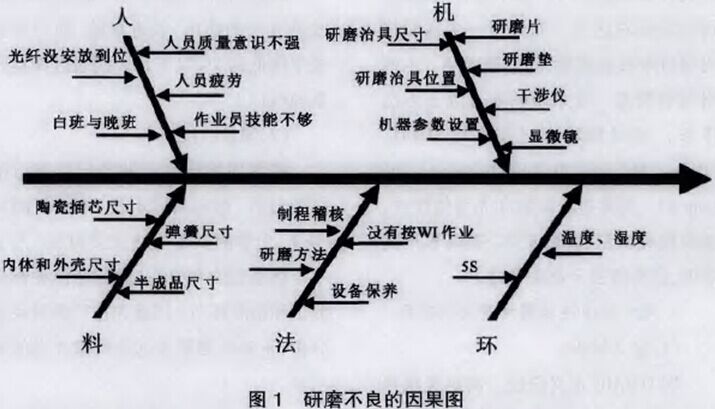
根據(jù)因果圖,并利用FMEA方法(Failure Mode and Effect Analysis),對各種影響因素進行評估,項目組最終確定了兩個影響光纖快速連接器報廢率高的主要因素,作為改進的重點:
①光纖連接器半成品尺寸偏小。
所謂光纖鏈接器的半成品,是將固化好了預埋光纖的陶瓷插芯和插芯基座壓接在一起所形成的半成品。經(jīng)過隨機抽樣測量,發(fā)現(xiàn)有41%的光纖連接器半成品尺寸比正常的尺寸小,這個尺寸偏小會導致研磨的時候研磨壓力不夠,形成APC角度偏小、曲率半徑過大和端面劃痕、裂紋。
②研磨片使用次數(shù)過多。
研磨片使用次數(shù)超限后,會導致研磨片的性能發(fā)生變化,可能引起各種不可預知的問題,包括端面的劃痕、凹點及凹陷和裂紋,干涉儀測試中的不規(guī)則曲率、APC角度偏小、頂點偏移。
4、改進階段
在經(jīng)過分析階段確定了關鍵的少數(shù)影響因素之后,需要針對這些因素來進行驗證和改進。
①光纖連接器半成品尺寸偏小的改進。
光纖連接器半成品是由陶瓷插芯和插芯基座壓接而成,現(xiàn)分別對陶瓷插芯外徑尺寸和插芯基座內徑尺寸做假設檢驗(假設檢驗的結果見表2)。 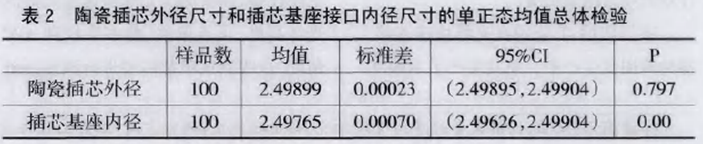
a、陶瓷插芯外徑尺寸的假設檢驗(標準尺寸為2.499±0.0005mm);
H0:這批陶瓷插芯的外徑尺寸為2.499mm ;
H1:陶瓷插芯的外徑尺寸不是2.499mm;
b、插芯基座內徑尺寸的假設檢驗(標準尺寸為2.49±0.01mm);
H0:這批插芯基座的內徑尺寸為2.49mm;
H1:插芯基座的內徑尺寸不是2.49mm。
從表2可以看出,陶瓷插芯外徑尺寸的P=0.797>0.05,所以接受Ho假設,認定這批來料的陶瓷插芯的外徑尺寸是2.499mm;插芯基座接口內徑尺寸的P=0.000<0.05,所以拒絕H0假設,認定這批來料的插芯基座接口的內徑尺寸不是2.49mm。
由此看來。插芯基座接口的內徑尺寸偏大是根本原因,其內徑尺寸95%的置信區(qū)間是(2.496,2.499),這個區(qū)間雖然在正常的尺寸范圍內,但是偏離了中心。在壓接過程中,壓接的壓力是根據(jù)陶瓷插芯2.499mm和插芯基座接口內徑2.49mm的標準設計的,如果插芯基座接口的內徑全部偏大,而遇上陶瓷插芯外徑偏小的情況,在同樣的壓力情況下,就有可能將陶瓷插芯壓力更深,導致光纖連接器半成品前部突出尺寸過小,最終的結果可能會導致在研磨的時候壓力過小,研磨成品不合格。
對于這個問題,最終解決辦法是:
a、通知供應商,要求供應商改進尺寸,重新供貨;
b、在產品線增加一個測量環(huán)節(jié),測量光纖半成品的突出尺寸,根據(jù)研磨治具的尺寸,這個光纖連接器半成品的前端尺寸定為9.5±0.05mm。
②研磨片使用次數(shù)過多的改進。
在研磨過程中有4種型號研磨片,只有4個步驟都結束后才能對光纖連接器進行參數(shù)測量,因此采用交叉排除驗證法。交叉排除驗證法的基本思想是,在保證其他3種型號研磨片不會超限使用的前提下,對剩下的這種型號的研磨片進行極限測量,通過采集的參數(shù)畫出圖表就可以直觀的看出所針對的這種研磨片的最佳使用次數(shù)。以SOHG研磨片作為第一個改進實例,在保證其他3種型號的研磨片不會超限使用的前提下,對SOHG研磨片進行極限測量,圖2是經(jīng)過5次測量實驗后得到的數(shù)據(jù)圖。
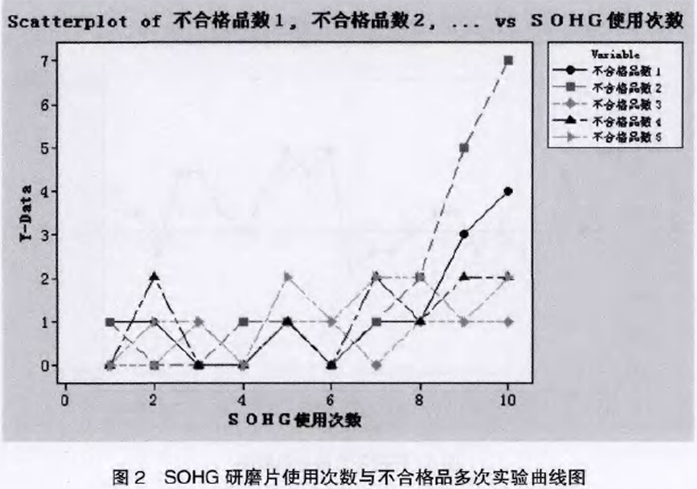
經(jīng)多次實驗,大部分SOHG研磨片都可以使用10次而不會影響成品質量,但有些SOHG研磨片在第9次出現(xiàn)了不合格品上升的拐點,考慮到批量生產,實驗實際上將SOHG研磨片使用次數(shù)定為8次。
基于同樣的方法,可以依次得到所有4種研磨片的最大使用次數(shù),通過多次排除檢驗,最終得到4種研磨片的最大使用次數(shù),即D30um為50次,D9um為30次,D1um為50次,SOHG為8次。
5、控制階段
控制階段需要有效控制影響響應輸出的關鍵影響因子,實現(xiàn)預防性控制。項目組將改進階段得到的措施用于實踐生產,然后監(jiān)控一些關鍵參數(shù),具體測量方法:
①每半小時測量5件光纖連接器半成品的前端尺寸,連續(xù)測量25組數(shù)據(jù)。將采集得到的數(shù)據(jù)繪成Xbar-R控制圖,光纖連接器半成品的控制目標為尺寸范圍9.5±0.05mm。
②每小時抽檢100件研磨成品,分別記錄不合格品數(shù)量,計算不合格率,連續(xù)記錄24小時,繪制計數(shù)型控制圖,其中研磨成品不合格率控制目標為7%。
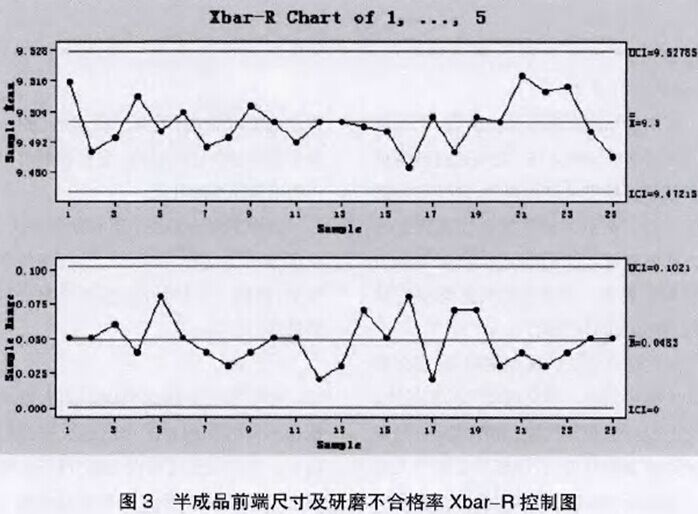
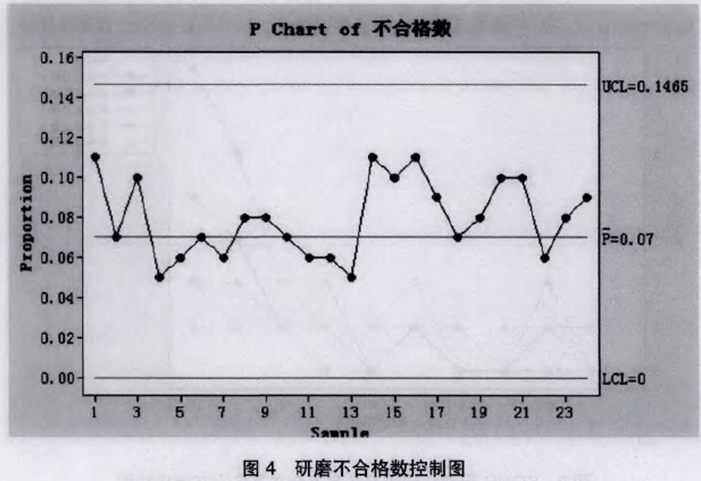
從圖3和圖4可以看出:所有點都在控制限內,這些點隨機分布在中心線周圍,并且沒有鏈、趨勢或者其他模式。
因此,當前過程是穩(wěn)定可控的,影響光纖快速連接器質量的兩項主要缺陷在改進后得到了很好的控制。