某設備公司重點型號產品導向筒零件的不合格品率為65%,其中因外圓(φ27.887mm)圓柱度(0.008mm)超差而引起的不合格品占90%,返修后仍有50%的零件報廢,從而嚴重影響了零件及產品的正常交付。為此,天行健管理公司針對該零件的加工工藝流程進行了分析,找出了外圓圓柱度超差的主要原因,制訂了改進方案,提高了導向筒外圓圓柱度的一次交檢合格率。
1、要將導向筒圓柱度0.008 mm的DPMO水平由585000降低到100000以下,改善率要達到90%。
2、制定方案,改進生產工藝,提高導向筒生產的合格率,降低返修、報廢率。
一、原因分析
為實現項目目標,成立了項目團隊,成員包括主管工藝員、檢驗員和操作工人等,團隊成員運用頭腦風暴方法,分析了導向筒的加工流程圖(如圖1所示),找出了19個潛在影響導向筒外圓圓柱度的因素。

圖1
團隊對這些潛在因素的影響程度給予評分,評分檔次分為無影響0分、不明顯1分、一般3分和嚴重9分,每個因素的所有得分相加,結果超過21分,則為重要因素(見表2)。
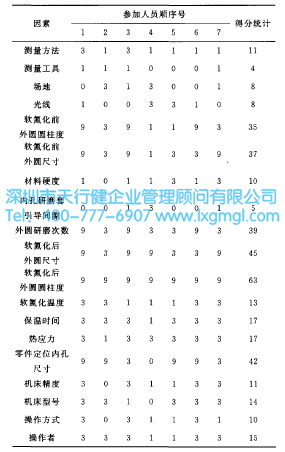
表2
通過評分,確定對導向筒外圓圓柱度有重要影響的因素有:軟氮化前、后的外圓圓柱度,軟氮化前、后的外圓尺寸,定位內孔尺寸和外圓研磨次數。后續工作就是進一步收集這些重要因素的數據,并進行統計分析,以確定關鍵的影響因素。
應用MINTAB分析工具,對收集的6個因素的數據進行分析,作出了矩陣圖(如圖3所示),根據矩陣圖的結果可以得出如下結論。
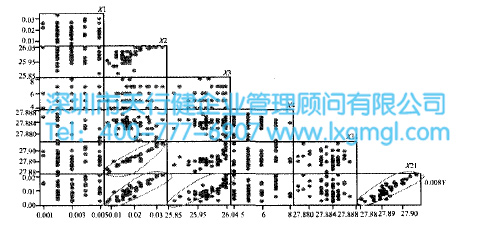
圖3
①軟氮化后外圓圓柱度(X2)與φ27.887mm外圓圓柱度(Y向0.008mm)間存在強正相關性;
②定位內孔尺寸(X3)與價φ27.887mm外圖圓柱度(x向0.008mm)間存在弱正相關性;
③軟氮化后外圓尺寸(X21)與軟氮化后外圓圓柱度(X2)間存在強正相關性;
④軟氮化后外圓尺寸(X21)與φ27.887mm外圓圓柱度(Y向0.008mm)間存在強正相關性。
通過這些因素進一步分析,作出了對φ27.887mm外圓圓柱度(0.008mm)實際影響的通用線形回歸模型圖(如圖4所示)。
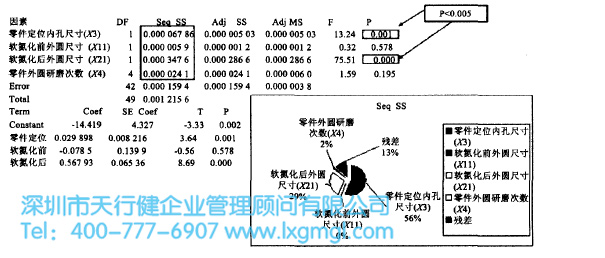
圖4
由圖4可以得出,軟氮化后外圓尺寸是影響外圓圓柱度的關鍵因素,它的影響率為29%;導向筒定位內孔尺寸也是影響外圓圓柱度的關鍵因素,它的影響率為56%。這2個因素的影響率合計為85%。導向筒軟氮化后外圓圓柱度超大,說明零件存在變形,變形過大會使后續工序無加工余量;另外,導向筒定位內孔尺寸超大,會使其最小壁厚尺寸要求無法保證,研磨外圓時無法定位。而軟氮化工序屬熱處理工序,導向筒變形無法避免,改進的方向應為控制或削弱這種變形。
二、改進和控制
項目目標改進的方向明確后,繼續收集數據。應用MINTAB分析工具,找到改進關鍵因素的方法,有針對性地制訂合理有效的措施并付諸實施。對于關鍵因素軟氮化后的外圓尺寸,采用分析確定流程改進的方法,將原來不進行控制的外圓尺寸現控制為<φ27.887mm,為實現此要求,新增加穩定處理工序。軟氮化工序新增專用工裝2D 413/016(此項工作由熱處理分廠負責完成)。將關鍵因素定位內孔尺寸進行改良,導向簡加工工藝流程改進前、后的對比(如圖5所示)。

圖5
另外,應加強工藝人員對現場加工情況的監控,保證措施的有效落實,并制訂導筒加工流程控制計劃表(見表6),即先通過工藝規程單,進行改進方案驗證,并將改進前、后外圓圓柱度的數據進行分析,控制和保持改進效果。
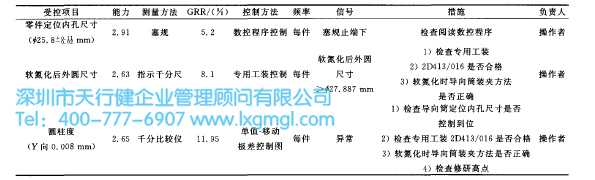
表6
三、結語
將改進后的工藝方案跟蹤03,04和06批零件生產過程進行驗證,將相關數據進行分析,外圓圓柱度工藝方案改進前、后結果的受控狀態(如圖7所示)。

圖7
改進后外圓圓柱度的流程能力分析(如圖8所示),由圖8能夠得出,改進后,φ27.887mm外圓圓柱度0.008mm的DPMO水平為3864.06,改善率達98%,達到了項目目標。說明了改進后的工藝方案能夠滿足導向筒外圓圓柱度的加工質量,能夠滿足產品生產要求,改進方案正式納入導向筒零件加工工藝規程中。
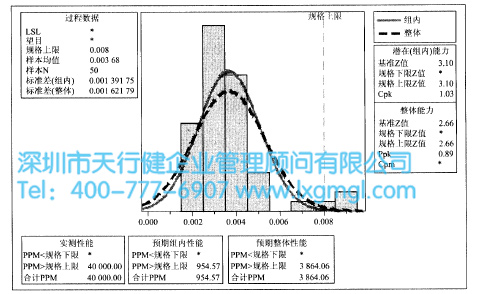
圖8
1、導向筒工藝改進后,φ27.887mm外圓圓柱度0.008mm的DPMO水平為3864.06,改善率達98%,達到了項目目標。
2、改進后的工藝方案能夠滿足導向筒外圓圓柱度的加工質量,能夠滿足產品生產要求。