該公司主要生產某公司筆記本外殼,外殼為鋁材需經過沖壓、CNC等一系列機械加工以及陽極氧化處理。在生產過程中異常較多,尤其是陽極處理后產品表面出現一種黑線缺陷,在白色底色上反差特別大,造成了大量產品報廢。該公司決定聘請天行健管理顧問公司全面推動六西格瑪管理,結合實際問題進行此項制程參數的設計,找出最關鍵的因素加以改進,提高效益。
1、集團內部成立處理技術委員會,成立多部門合作的改善小組專門進行表面處理專業技術的開發及傳承,以及相關疑難問題的探討
2、應用六西格瑪DMAIC解決該公司鋁合金參數的設計問題
3、避免拋光時材料雜質脫落,降低不良品、降低廢品率
4、制訂合理的制程參數,在一個月左右提升良率到95%以上
5、提高化學拋光制程中工藝質量,提高公司全年經濟效益
全面品質管理的觀點現已逐漸在全球范圍內獲得認可和傳播,六西格瑪可以看作是全面質量管理的一種繼承性新發展,隨著管理體制的日益成熟,六西格瑪開始跨越國界和行業領域,在全世界展現其巨大的魅力。
該公司采用的是陽極自動線,制程時間及槽液溫度只需程式設定。鋁的陽極氧化是通過化學及電化學的方法在鋁合金表面形成陽極氧化膜從而達到耐蝕、增加硬度和耐磨性、裝飾、提高有機涂層和電鍍層附著性、絕緣、增加透明度和其他功能效果的特性。
為了讓表面有均勻的顆粒感,故在前工段加入了噴砂的工藝,而化學拋光使得砂面紋路鈍化,光澤柔和。化學拋光法是借助于金屬微觀表面在化學溶劑中的選擇性溶解作用,即微觀粗糙表面凸起部分的溶解速度高于凹陷部分的溶解速度,從而達到光潔度要求的一種表面處理方祛,化學拋光的機理模型如下圖所示。
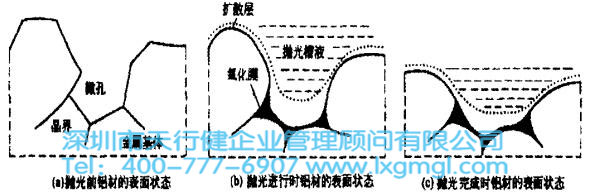
圖 化學拋光的機理模型
一、該公司目前存在的問題
是表面處理良品及不良品的對比照片,可以明顯看到在產品表面有一條或多條異色的線條。實際是一連串的形狀不規則的小凹坑組成,天行健管理顧問公司從不良現象來分析,認為有可能是在化學拋光制程中工藝不當,造成過拋光或拋光時材料雜質脫落造成。
二、問題的定義與分析
六西格瑪DMIAC這一體系是由五部分組成的閉環系統,它是為了提高和改進己有產品和過程且以數據驅動的質量方法。主要包括以下幾個階段:定義(DEFINE),測量(MEASURE),分析(analyze),改進(IMPROE-MENT),控制(CONTROL)。
三、應用六西格瑪DMAIC解決該公司的問題步驟
首先成立多部門合作的改善小組,由品工主導、制程工程師、工藝工程師、品管等成員共同設計制程參數。天行健管理顧問公司提出的目標是制訂合理的制程參數,在一個月左右提升良率到95%以上。
D階段:問題的定義
正常情況下陽極表面處理良率可以穩定在95%-98%之間,但是參考原定的表面處理工藝,基本上都有10%-30%的不良品。
M階段,問題的測試:
產品經過整個表面處理工藝后,通過目視檢驗外觀。檢驗條件:在800lux-11OOlux(勒克司)的照明下,翻轉180度,眼睛和產品距離30cm。為了避免人工錯判,我們設計了透明比對板,凡有25%灰度無法遮蔽且長大于12mm,寬大于0.1 mm的黑線則判定為不良品。我們分別讓3名品管檢驗同一批100pcs產品,其中5件不良品,對判定的重復性和再現性進行了計算,AR&R=95.2%,因為此數值大于95%,可以接受此測量方法的可靠性。
A階段,分析階段:
我們經過對加工過程中的各種不同變量、參數的整理,進行魚骨綜合分析了化學拋光工站的輸入變量的影響,于是我們設計了多種對比試驗和正交試驗,對比調整后的結果,通過排查法,發現此不良現象產生的原因有以下三點:
第一,與陽極處理設備有較大關聯。該產品在試做線(小槽)試樣時良率較高,但是十月份一轉入正式量產后在量產線生產時(大槽)黑線不良有提升趨勢。
第二,與槽液的配比有所關聯。重新更換槽液或者加槽液調整化學拋光槽中的mp/s值(磷硫酸比值),良率有所變化。
第三,與制程參數有較大關聯,通過調整化拋時間和槽液的溫度,良率有較大的變化。
基于以上現象天行健管理顧問公司分析原因主要有幾點:
第一、因為槽液主要配比是磷硫混合酸,陽極槽是不銹鋼制作,對于表面有防腐蝕需要的幾個槽,表面做了鐵氟龍處理。而大槽使用壽命近3年,可能部分表面鐵氟龍脫落,槽液與設備發生反應,從而在槽內引入了鐵離子,影響良率。
第二、化學拋光槽液中的磷酸和硫酸的比值、A13+含量以及化拋的時間和槽液的溫度對黑線異常的影響有較大的影響。
事實上,鋁合金表面腐蝕坑的形成具有必然性鋁合金中微量元素的存在,當材料中微量元素分布不均并富集表面(或作為強化相析出)時,由于金屬活性存在的差異,與槽液反應有快有慢,從而形成腐蝕坑。腐蝕坑的大小與微量元素富集程度有關。合金材料必然存在不均勻腐蝕形成的腐蝕坑。關鍵是腐蝕坑是否大到陽極后能目視看得到。
化學拋光過程可以歸納為:鋁的酸性侵蝕過程→鈍化過程→黏滯性擴散層的擴散過程。
由于陽極槽液中不活潑金屬離子的存在會加速活潑金屬的溶解;而溶解過程的快慢也會產生腐蝕坑,同時被置換上去的不活潑金屬與周圍發生原電池反應加速鋁的溶解腐蝕坑被擴大化。因此通過上面的天行健管理顧問公司專家分析認為需在減少雜質以及制程條件調節上來控制。
I階段,改進階段
針對分析階段發現的兩個問題,用DOE的辦法,對化拋工序進行了參數優化。在DOE中選擇了四個變量因子,每個變量兩個水平。
輸入是槽液磷酸/硫酸比mp/s、槽液溫度、反應時間是4因子2水平的部分因子正交試驗。輸出變量是陽極產品良率。
從結果中找到了2個對黑線產生有顯著影響的變量,并使用MINITAB的優化器功能對參數進行了優化。最終,磷硫比mp/s控制在3.5-4.2, Al3+控制在15%到30%,進行測試發現溫度控制在80-88℃,時間控制在60到90秒較合理。通過最終試驗我們得到了最穩定的數值,把溫度控制在85度,時間控制在70s。在新的設置數值下,又進行了兩次重復試驗,結果都較理想。
C階段,效果控制和跟蹤
最后,新制了化學拋光槽并對鍍鐵氟龍的所有工序:前處理-除塵-噴涂-烘烤-冷卻-下料進行跟蹤檢驗,確認無誤后進行了小批量生產。對比發現,不良狀況有所改善。
在其他條件不變的情況下,采用兩個槽進行生產。發現表明兩個槽是有區別的,在重復驗證后,對原化學拋光槽進行更換,并制定化學拋光槽鐵氟龍覆蓋狀況的內容記錄到設備月度保養和正常點檢的項目中。這樣就保證了在點檢時能夠及時發現問題,避免不良的化拋產品到最后道工序時才發現。
通過天行健管理顧問公司的研究,運用對比試驗(BVs .C)和正交試驗(DOE),共計運行64組試驗,從大量的試驗結果和數據中,得到了有效的改進方法得到顯著的效果。
1、成立了多部門合作的改善小組,由品工主導、制程工程師、工藝工程師、品管等成員共同設計制程參數。
2、制訂合理的制程參數,得到了有效的改進,在一個月內廢品率從1O%,下降到了5%。
3、經過三個月的工作,最終廢品率在陽極工段下降到2%以下的水平。
4、大力提高了經濟效益,經濟效益在每年900萬元以上。