在六西格瑪導入初期,天行健咨詢專家先在該企業進行了系統的六西格瑪培訓,讓企業員工詳細了解六西格瑪,明確知道六西格瑪的實施方法及六西格瑪所能帶來的收益效果。經過一周的培訓后,六西格瑪項目正式啟動。
一、定義階段
1、項目選題:
天行健咨詢專家與項目小組經過討論及分析,從公司戰略和提高顧客滿意度出發,確定選題。項目小組擬通過提高自動焊接的質量水平,降低焊接缺陷,減少保修成本,提升企業質量品牌,支撐企業實現進入全國空調制造企業前三名,并與國際著名企業品牌相抗衡的戰略目標。
2、改進機會:
項目小組進而分析了該項目的改進機會。當前,自動焊接工序造成的缺陷占70%左右,企業每年在這方面的直接經濟損失就達到1000萬元:當前DPHU為6,按每個產品上有40個焊點計算,目前質量水平為DPMO=1500,西格瑪水平為4.47。企業高層要求該關鍵工序的DPHU應在2以下。
3、項目范圍:
項目小組同時界定了該項目的項目范圍。該過程的SIPOC圖如圖1所示,同時,根據項目特點及項目的可操作性兩方面考慮,確定項目的范圍是從沖片工序開始一直到產品檢驗入庫為止。
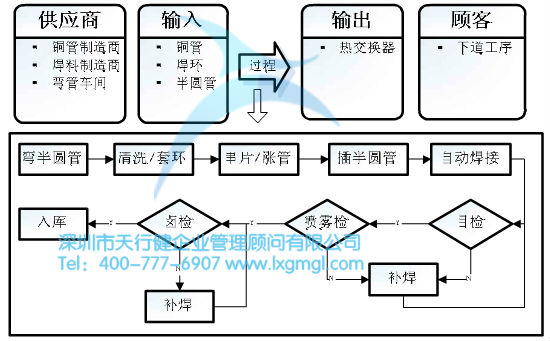
圖1
此外,項目小組還詳細制定了項目的時間安排及預期成果。
二、測量階段
測量階段的主要任務是確認測量系統的能力是否充分,必要時對測量系統進行改善。并在此基礎上測定相關指標的當前績效水平。
在了解過程的基礎上,找出影響焊接不良的主要因素,即找出影響CTQ(Y)的主要因素(x)。為此,小組成員根據工程經驗,確定主要影響因素為半圓管中心距及自動焊工序。
半圓管的彎管過程由彎管機完成,再由測量人員利用測量儀器對半圓管中心距進行測量。而對于焊接缺陷的檢驗則是依靠檢驗員目視檢驗進行的。在DMAIC的測量階段,再做進一步的數據分析之前,應該首先確保相關測量系統的能力充分。因此,應對這兩個測量系統分別進行分析。
1、半圓管中心距測量系紛分析
隨機選兩名測量者,并抽取10個半圓管作為樣品,將這10個樣品隨機分配給兩名測量者進行測量,并且使每位測量者對每個零件重復測量3輪。測量數據如表1所示。半圓管的公差為25.4士0.1。

表1
對表1中的數據進行分析,結果如表2所示。由此結果知,該測量系統的重復性與再現性百分比(R&R%)為25.8%,精度公差比(P/T%)為43.85%。顯然,兩者均超過了10%,表明測量系統能力不足。
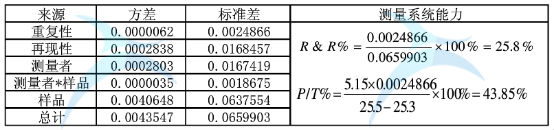
表2
進一步分析會發現,該測量系統的變異主要源于再現性誤差。項目小組經過研究發現,再現性較高的原因是測量作業標準不規范,為此,小組重新制訂測量作業標準,并
對所有測量人員進行針對性地培訓。然后,再次按照上述過程進行測量系統分析,
結果為R&R%=7.2%, P/T%=9.47%。此時測量系統能力可以接受。
2、彎管機過程能力分析:
在確定測量系統能力充分后,對彎管機過程能力進行評定。項目小組在生產過程穩定條件下,隨機抽取100件樣品,并進行分析,如圖2所示。此時,計算得到Cp= 0.61,Cpk=-0.56。顯然,過程能力嚴重不足。
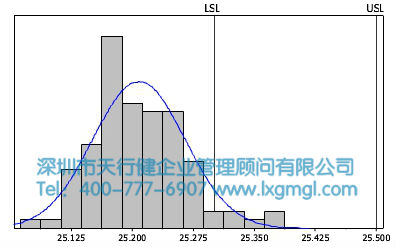
圖2
三、分析階段
1、彎管機能力不足原因分析
在測量階段,測量彎管過程的過程能力為Cp=0.61, Cpk=-0.56,過程能力嚴重不足。對該過程此前該企業從未進行過類似測定,但根據小組成員已知的工程經驗,彎管機模具的尺寸誤差對半圓管中心距有著直接的影響。根據這個思路,小組對彎管機模具進行測定,發現所使用的模具的尺寸偏大,不符合設計要求。
2、焊接缺陷原因分析
為找出影響焊接缺陷的主要原因,小組進行了因果分析,如圖3所示,并利用多輪投票法確定主要影響因素。
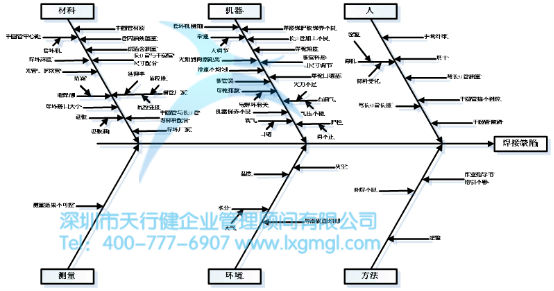
圖3
經過分析,確定影響焊接缺陷可能的主要原因有:后排槍的距離、后排槍的角度、前排槍的距離、前排槍的角度、后排槍的氧氣量、前排槍的氧氣量,為方便討論,依次記為A、B、C、D、E、F。
四、改進階段
1、彎道機改善
根據分析結果,對彎管機的模具進行調整,使所用的模具尺寸符合設計要求。并在此基礎上,再次對該改進后的彎管過程進行過程能力分析,如圖4所示,計算得到Cp=1.41,Cpk=1.15,此時,彎管機過程能力充分。
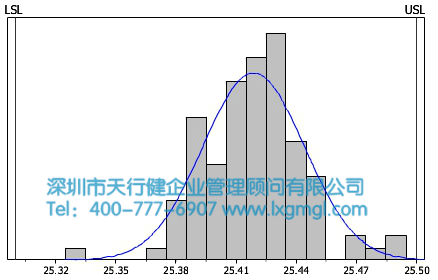
圖4
2、自動焊工藝參數優化
在分析階段,確定了影響焊接缺陷的主要原因,為了進一步確定焊接缺陷與各影響因素間的關系,將焊接缺陷的每百件產品上的缺陷數(DPHU)視為響應輸出Y,借助于試驗設計(DOE)。由于因子較多,同時考慮到試驗成本,選定2(6-2)部分因子試驗方案,并安排了3次中心點試驗。各因子的位級取值如表3所示,試驗方案及試驗結果如表4所示,而該部分因子試驗的分辨力為IV,其混淆結構則如表5所示。
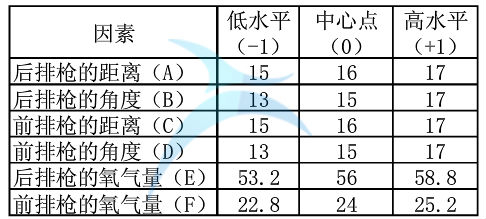
表3
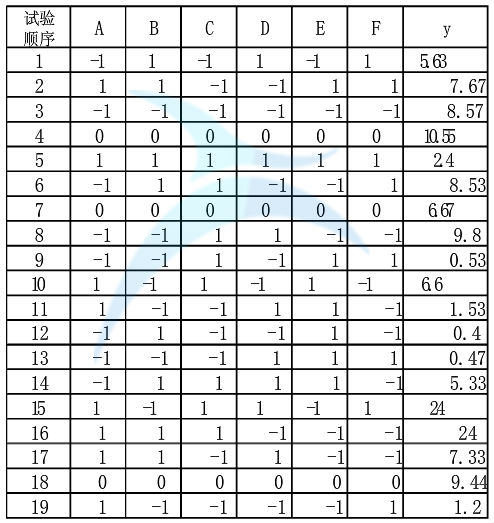
表4
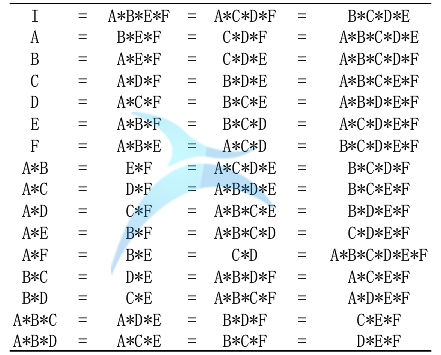
表5
根據表4中得到的各次試驗的結果進行分析,方差分析結果如表6所示,各因子效應及顯著性分析如表7所示。由表6、表7可以看出,模型的曲性不顯著,主因子中A、C、E三個因子影響顯著,此外,交互作用A*C、B*D、A*B*D對響應的影響顯著。但是,考慮到部分因子存在混淆的情況,所以,以上分析出的因子是否合理還要看混淆結構。結合表5中的混淆結構,可以看出,主因子和3階和4階交互作用混淆,這種情況下,如果因子顯著,通常認為是主因子顯著,因此,可以認為A、C、E三個因子的影響顯著。再看A*C,它與E*F及兩4階交互作用混淆,通常在實際工程問題中,高階交互作用不顯著,因此可以先不考慮兩個4階交互作用,而A*C與E*F中,由于A*C的親本因子A和C均顯著,所以認定A*C顯著應合理。對于B*D,不考慮與高階交互作用的混淆,其與C*E混淆,而C*E的親本因子C和E均顯著,所以認定C*E顯著更為合理。對于A*B*D這個3階交互作用,它與A*C*E、B*C*E、D*E*F混淆,其中,A*C*E的親本因子A、C和E均顯著,所以認定A*C*E顯著更為合理。

表6
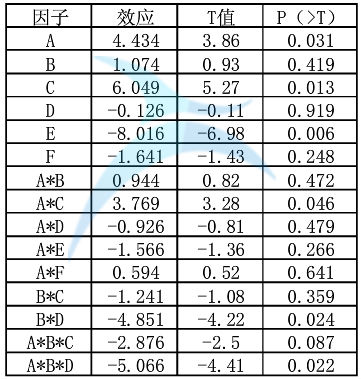
表7
根據上述,分析,確定顯著因子為A、C、E、A*C、C*E、A*C*E。據此,將模型中的非顯著項剔除,并重新擬合模型,進行分析,得出二次擬合后各因子效應及顯著性如表8所示。對模型適合性作進一步的分析發現,模型的適合性沒有存在問題。
通過試驗設計及分析,可得出焊接缺陷DPHU與上述各因子間有如下關系:
Y=7.403+2.217A+3.024C-4.008E
+1.884A*C-2.426C*E-2.533A*C*E
試驗設計的目標是極小化DPHU,根據上述模型得到的最優工藝參數為:
A=-1,即后排槍的距離為15cm;
C=-1,即前排槍的距離為15cm;
E=1,即后排槍的氧氣量為58.8升/分。
小組按照上述分析結果對工藝參數進行調整,并對結果加以驗證。在上述參數條件下生產了200臺蒸發器,檢測得DPHU可以控制在0.05以內。過程質量顯著提高。
五、控制階段
彎管機過程
在作業指導書中,增加彎管機換模時必須進行模具尺寸的測定并填寫換模記錄表,以確保模具尺寸符合要求。
對彎管過程輸出的半圓管的中心距建立X-R控制圖(如圖5),對彎管過程進行監控。
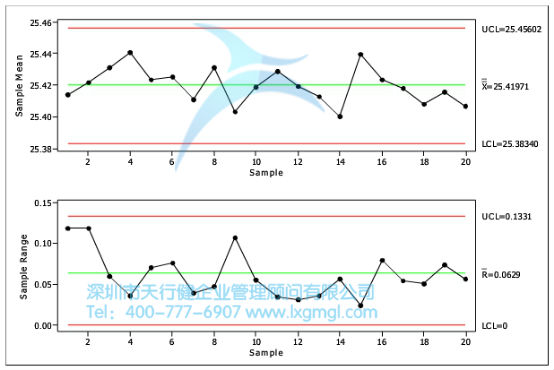
圖5