精益六西格瑪是將六西格瑪方法與精益生產(chǎn)方式二者相結(jié)合得到的一種管理方法,即Lean Six Sigma簡稱 LSS。它通過提高顧客滿意度、降低成本、提高質(zhì)量、加快流程速度和改善資本投入,使股東價(jià)值實(shí)現(xiàn)最大化 。精益六西格瑪管理的目的是通過整合精益生產(chǎn)和六西格瑪管理,吸收兩種生產(chǎn)模式的優(yōu)點(diǎn),彌補(bǔ)單個(gè)模式 的不足,達(dá)到更佳的管理效果。精益六西格瑪不是精益生產(chǎn)和六西格瑪?shù)暮唵蜗嗉樱嵌叩幕ハ嘌a(bǔ)充、 有機(jī)結(jié)合。
傳統(tǒng)六西格瑪項(xiàng)目主要解決與變異有關(guān)的復(fù)雜問題,例如控制一個(gè)過程的產(chǎn)品一次通過率:而精益六西格瑪項(xiàng)目解決的問題不僅包括傳統(tǒng)六西格瑪所要解決的問題,而且要解決那些與變異、效率等都有關(guān) 的“綜合性”復(fù)雜問題,例如不但要控制一個(gè)過程的產(chǎn)品一次通過率,還要優(yōu)化整個(gè)生產(chǎn)流程,簡化某些動(dòng) 作,縮短生產(chǎn)周期。歡迎關(guān)注(天行健管理咨詢專業(yè)做精益六西格瑪管理培訓(xùn)咨詢與項(xiàng)目輔導(dǎo)服務(wù))
因此,如何將精益六西格瑪管理正確的運(yùn)用到實(shí)際生產(chǎn)過程中,解決具體問題,是不少 企業(yè)面臨的一個(gè)難題。本文以縮短X機(jī)箱的交付周期為例,對(duì)精益六西格瑪管理方法的實(shí)施和應(yīng)用進(jìn)行探討。
精益六西格瑪項(xiàng)目背景
成都某電子股份有限公司是研制生產(chǎn)飛機(jī)大氣數(shù)據(jù)系統(tǒng)、飛行數(shù)據(jù)集成系統(tǒng)、無線數(shù)據(jù)通信等航空電子及 傳感器的機(jī)載設(shè)備骨干企業(yè)。公司下設(shè)的航空特種設(shè)備廠(以下簡稱特設(shè)廠),主要承擔(dān)公司的航空機(jī)箱類產(chǎn) 品、航空特種設(shè)備類產(chǎn)品的零組件生產(chǎn)制造任務(wù)。航空機(jī)箱產(chǎn)品作為分廠的重點(diǎn)發(fā)展產(chǎn)業(yè)之一,對(duì)于分廠“ 十二·五”發(fā)展目標(biāo)的實(shí)現(xiàn)起著重要作用。
但是由于分廠內(nèi)部業(yè)務(wù)流程不清晰、產(chǎn)品合格率不高,使得航空 機(jī)箱類產(chǎn)品經(jīng)常延遲交付。為了滿足客戶需求,立足分廠發(fā)展戰(zhàn)略,結(jié)合分廠IBSC指標(biāo)分解,通過市場分析 、產(chǎn)品簇圖、顧客voc識(shí)別等方法,確定對(duì)整個(gè)航空機(jī)箱產(chǎn)品進(jìn)行流程改善。以此提升工藝技術(shù)水平,提高產(chǎn) 品合格率,提高產(chǎn)品生產(chǎn)效率和計(jì)劃完成率,滿足客戶需求,并形成機(jī)箱產(chǎn)品的市場核心競爭力,擴(kuò)大分廠 的經(jīng)營指標(biāo)規(guī)模和潛在市場。
組建項(xiàng)目團(tuán)隊(duì)(Step I )
首先根據(jù)確定的LSS項(xiàng)目,成立了跨部門的項(xiàng)目團(tuán)隊(duì),主要有分廠領(lǐng)導(dǎo)、財(cái)務(wù)人員、技術(shù)人員、生產(chǎn)管理和操 作人員組成。
組織機(jī)構(gòu)調(diào)整(Step 2 )
以前分廠的機(jī)構(gòu)設(shè)置按照傳統(tǒng)模式,在整個(gè)產(chǎn)品實(shí)現(xiàn)的價(jià)值鏈中,技術(shù)人員和生產(chǎn)管理人員是分離設(shè)置(見圖 I)。
技術(shù)人員和生產(chǎn)管理分離機(jī)構(gòu)設(shè)置模式,使得現(xiàn)場的等待時(shí)間中約30%是等待技術(shù)質(zhì)量問題的處理,通常 技術(shù)人員不能及時(shí)有效處理現(xiàn)場技術(shù)質(zhì)量問題,需要計(jì)劃組長與技術(shù)組長溝通協(xié)調(diào)。跨部門的管理模式常常 造成生產(chǎn)信息傳遞錯(cuò)誤,問題處理時(shí)間滯后。為了減少技術(shù)質(zhì)量問題處理的等待時(shí)間和提升技術(shù)人員的現(xiàn)場 處理能力,決定將技術(shù)人員調(diào)配至生產(chǎn)現(xiàn)場任職生產(chǎn)工程師,與計(jì)劃管理機(jī)構(gòu)合并(見圖2),避免生產(chǎn)和技術(shù) 之間的互相推諉,從而減少生產(chǎn)過程中的等待。
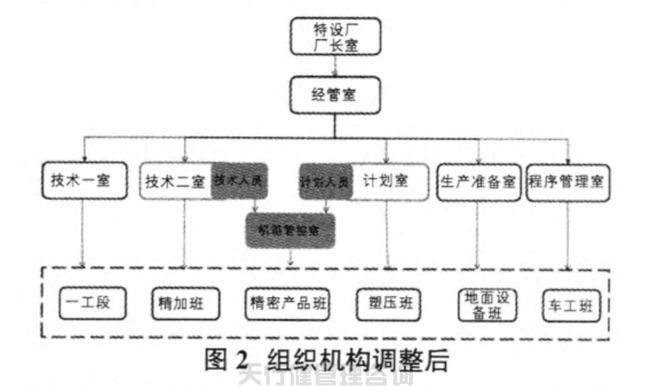
在整個(gè)項(xiàng)目的實(shí)施過程中,任何的變革和改變都會(huì)觸及相關(guān)方的利益,領(lǐng)導(dǎo)的參與和支持變革是至關(guān)重 要的。古人云“上下同欲者勝”,目標(biāo)一致的團(tuán)隊(duì)往往能夠事半功倍。QxA=E是我們所學(xué)習(xí)的變革精髓,任何 變革除了變革本身的“Q”以外.參與變革的參與者的“A”也至關(guān)重要,參與者對(duì)變革的思想統(tǒng)一認(rèn)識(shí)是基礎(chǔ) 。因此,在進(jìn)行機(jī)構(gòu)調(diào)整后需根據(jù)SIPOC圖對(duì)利益相關(guān)方進(jìn)行分析,分析結(jié)果表明參與者90%支持進(jìn)行組織機(jī) 構(gòu)調(diào)整,思想達(dá)到統(tǒng)一。
流程改善(Step 3 )
由LSS黑帶牽頭,對(duì)產(chǎn)品實(shí)現(xiàn)的整個(gè)流程進(jìn)行項(xiàng)目管理.制定項(xiàng)目管理里程碑,使用LSS的VSM等工具和方法.有 計(jì)劃、有目的、有步驟、系統(tǒng)的進(jìn)行流程梳理和改善。
1.項(xiàng)目定義
X機(jī)箱是為某重點(diǎn)型號(hào)配套的鑄造鋁合金機(jī)箱,根據(jù)數(shù)據(jù)統(tǒng)計(jì),自2011年以來.產(chǎn)品的FTY為60%,廢品率12%, 加工周期長,加工費(fèi)用較高。屢次延遲交付甚至影響某主機(jī)廠所配套,引起客戶嚴(yán)重抱怨。
通過6個(gè)月的流程梳理和改善,將X機(jī)箱的交付周期由45-84天降低至30-35天,F(xiàn)TY由60%提升至92%,月產(chǎn) 出12-15臺(tái),滿足客戶需求。
2.確定項(xiàng)目里程碑
項(xiàng)目管理的精髓是系統(tǒng)思考和項(xiàng)目受控,團(tuán)隊(duì)成員根據(jù)現(xiàn)場生產(chǎn)情況和客戶需求情況。制定了項(xiàng)目里程碑(見圖3),以保證能夠按時(shí)完成目標(biāo)值。
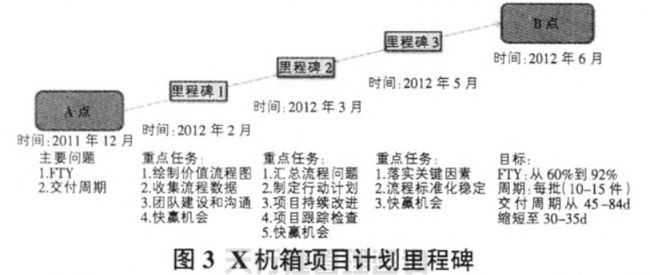
精益的五大原則是價(jià)值、價(jià)值流、流動(dòng)、拉動(dòng)和完美,它能夠使我們的企業(yè)“瘦身”,降低成本,改善質(zhì)量 和縮短周期。價(jià)值流是為客戶定義、創(chuàng)造、生產(chǎn)和交付價(jià)值所使用程序的綜合,價(jià)值流管理是對(duì)價(jià)值流的識(shí) 別、診斷、改進(jìn)和設(shè)計(jì),其目的是改善價(jià)值流的有效性(質(zhì)量),提高價(jià)值流的效率(流量),增強(qiáng)價(jià)值流的生 命力(適應(yīng)性)。
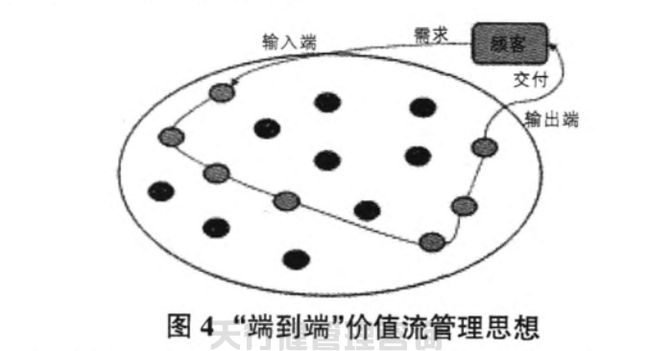
項(xiàng)目團(tuán)隊(duì)成員按照“價(jià)值流始于顧客,止于顧客”的系統(tǒng)思維(見圖4),從顧客需求末端出發(fā),到滿足顧 客需求的末端去。根據(jù)現(xiàn)場情況,用價(jià)值流程圖的分析方法,來進(jìn)行流程問題梳理和診斷。
診斷流程,若只解決流程中存在的共性問題或是只解決個(gè)性問題,流程得不到顯著的改善。需對(duì)流程進(jìn) 行全面優(yōu)理后,首先解決共性問題,然后抓住最典型的個(gè)性問題加以解決,并在隨后的工作中,將個(gè)性問題 改善的成果加以推廣,逐漸將個(gè)性問題全面解決。

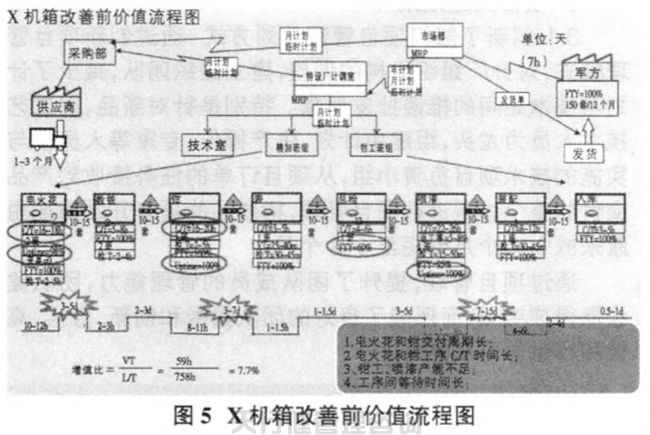
據(jù)此團(tuán)隊(duì)成員用價(jià)值流程圖分析方法(見圖5<1,2部分>),首先對(duì)信息流中技術(shù)現(xiàn)場處理問題等待時(shí)間長 和計(jì)劃目視不顯現(xiàn)的共性問題進(jìn)行梳理。其次根據(jù)VSM圖和客戶需求節(jié)拍,收集數(shù)據(jù)分析各工序的C/T時(shí)間(圖6),進(jìn)行工序產(chǎn)能分析,分析X機(jī)箱生產(chǎn)流程中存在的個(gè)性問題。經(jīng)過流程梳理,發(fā)現(xiàn)的主要問題如下。
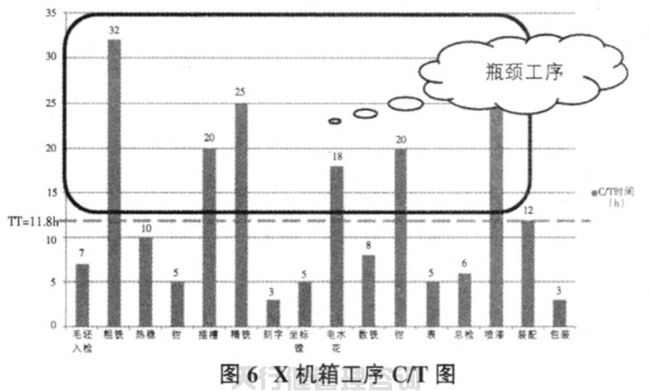
共性問題:①技術(shù)處理現(xiàn)場等待周期長;②計(jì)劃管理目視化不顯現(xiàn)。
產(chǎn)品加工個(gè)性問題:①粗鐵加工周期長;②插槽加工周期長;③精鐵加工周期長;④電火花加工周期長;⑤鉗工加工周期長;⑥噴漆加工周期長;⑦檢測(cè)周期長;⑧工序間等待時(shí)間長。
4.問題分解及子項(xiàng)目的管理
對(duì)共性問題主要采取WO等工具方法進(jìn)行改善.對(duì)于個(gè)性問題則根據(jù)X機(jī)箱的流程為研究對(duì)象,對(duì)其中的問題進(jìn)行分解并加以改善(見圖7 ).
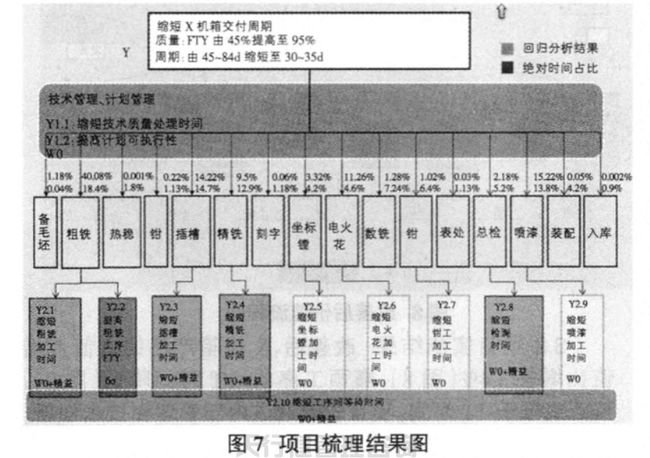
改善主要從工藝技術(shù)、流程優(yōu)化、提高加工合格率、工藝裝備、計(jì)劃管理、環(huán)境改善六個(gè)方面來展開,主要進(jìn)行改善的子項(xiàng)目行動(dòng)計(jì)劃如表1、表2。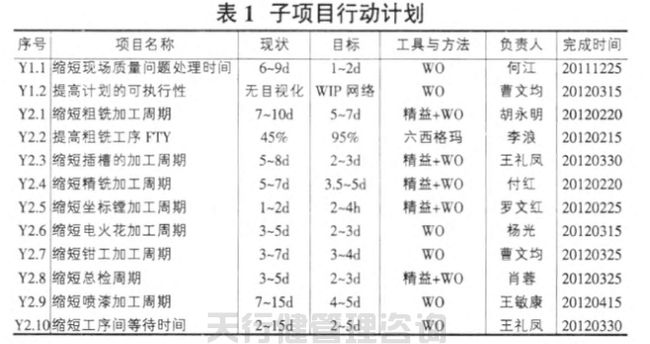
因?yàn)樽禹?xiàng)目較多,需要進(jìn)行項(xiàng)目管理,協(xié)調(diào)所有的子項(xiàng)目順利進(jìn)行。為此,分廠采用了一頁紙的項(xiàng)目管理方式,保障了子項(xiàng)目按行動(dòng)計(jì)劃順利開展。表2展示的是黑帶項(xiàng)目的一頁紙項(xiàng)目管理,對(duì)于下分的每個(gè)子項(xiàng)目也采用了這種方式進(jìn)行項(xiàng)目的統(tǒng)籌管理與推進(jìn),取得了明顯的效果。
5.子項(xiàng)目的輔導(dǎo)與改善要點(diǎn)
在項(xiàng)目實(shí)施過程中,運(yùn)用團(tuán)隊(duì)工作法以及精益六西格瑪?shù)母鞣N工具與方法,子項(xiàng)目在預(yù)期內(nèi)完成了改善。整個(gè)項(xiàng)目的主要改善點(diǎn)如下:
①工藝技術(shù)及技術(shù)管理方面。
毛坯改善:鑄件毛坯增加工藝凸臺(tái),作為定位、裝夾、加工、檢驗(yàn)的基準(zhǔn)。通過毛坯改善,提高了粗、精銑加工的FTY,縮短了粗、精銑工序的C/T時(shí)間和交付時(shí)間;縮短了鉗工工序的C/T時(shí)間;減少了銑加工中的零件找正等不增值時(shí)間。工裝改善:通過工藝裝備改善,減少了銑加工中的零件多面找正、重復(fù)定位等不增值時(shí)間。縮短了粗、精銑工序的C/T時(shí)間和交付時(shí)間;縮短了鉗工工序的C/T時(shí)間;減少了插槽工序的C/T時(shí)間和找正時(shí)間;取消了坐標(biāo)鏜工序。
②計(jì)劃管理方面。
為了提高班組與生產(chǎn)準(zhǔn)備計(jì)劃的一致性,縮短零件周轉(zhuǎn)中不增值部分,項(xiàng)目負(fù)責(zé)人組織相關(guān)人員進(jìn)行群策群力,共同分析討論。建立WIP信息網(wǎng)絡(luò)平臺(tái),加強(qiáng)計(jì)劃管理的目視化和顯性化,推廣計(jì)劃管理的色標(biāo)管理,班組計(jì)劃反饋管理等模式。同時(shí),輔以現(xiàn)場6S管理,提高了計(jì)劃的可執(zhí)行性。
③其他方面。
為了讓團(tuán)隊(duì)成員能按時(shí)完成所有子項(xiàng)目,在項(xiàng)目的實(shí)施過程中,積極進(jìn)行團(tuán)隊(duì)成員培訓(xùn),以及對(duì)外協(xié)廠家進(jìn)行技術(shù)和管理支持,以提高整個(gè)項(xiàng)目的外部和內(nèi)部資源的同步提升。
在子項(xiàng)目的改善過程中,大量采用了要因分析、流程能力分析、測(cè)量系統(tǒng)分析、風(fēng)險(xiǎn)分析、假設(shè)檢驗(yàn)、回歸分析、群策群力、團(tuán)隊(duì)工作法等六西格瑪工具和方法。
6.子項(xiàng)目改善關(guān)鍵要點(diǎn)及控制計(jì)劃
對(duì)所有的子項(xiàng)目改善完成后,對(duì)關(guān)鍵因素進(jìn)行有效控制,是長久保持成果的好辦法。據(jù)此制訂了詳細(xì)的控制計(jì)劃,在現(xiàn)場實(shí)施見項(xiàng)目控制計(jì)劃表(表3)。
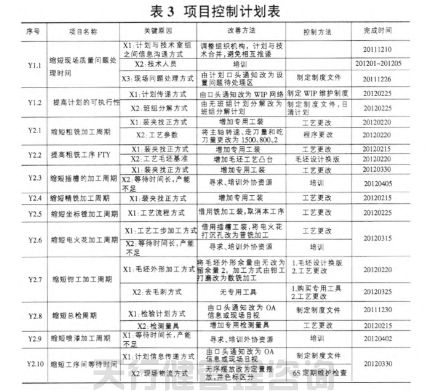
改善成果推廣,持續(xù)流程改善(Step 4 )
1.子項(xiàng)目改善成果在內(nèi)部推廣
縮短X機(jī)箱生產(chǎn)周期項(xiàng)目,改善的是全流程的價(jià)值鏈。鑄件毛坯基準(zhǔn)統(tǒng)一方法,毛坯加工找正工裝,插槽工裝以及工裝的設(shè)計(jì)思想和方法對(duì)其它同類型的鑄件機(jī)箱生產(chǎn)奠定了基礎(chǔ)和積累了經(jīng)驗(yàn)。
由于鑄件機(jī)箱加工的工藝流程比較相似,所以該項(xiàng)目具有了推廣性。對(duì)于在整個(gè)生產(chǎn)流程中提煉并形成的鑄件高精度精密加工工藝也成為分廠的核心工藝技術(shù)之一。目前,已推廣至分廠的34個(gè)機(jī)箱生產(chǎn)型號(hào)中,提高了其它型號(hào)機(jī)箱的生產(chǎn)效率和產(chǎn)品質(zhì)量。
在整個(gè)流程實(shí)施過程中,也逐步積累和提升了工藝技術(shù)管理和項(xiàng)目策劃的能力,對(duì)外部供應(yīng)鏈的培育和培養(yǎng)也形成了分廠的固定流程和步驟,為其它項(xiàng)目的策劃提供了有益的組織模式和方法。
2.項(xiàng)目梳理與改善方法推廣到其它流程
成果的推廣應(yīng)用只是局部的改善應(yīng)用,不同工種、不同流程內(nèi)在的問題,需要進(jìn)行詳細(xì)的梳理和系統(tǒng)全面的改善,才能產(chǎn)生明顯的效果。
對(duì)X機(jī)箱生產(chǎn)流程進(jìn)行梳理后,分廠對(duì)其它機(jī)箱產(chǎn)品生產(chǎn)流程進(jìn)行了梳理,隨后又對(duì)訂單管理流程進(jìn)行了梳理,并不斷的對(duì)流程進(jìn)行優(yōu)化和PDCA循環(huán),正是沿用了LSS流程梳理的方法與工具。
3.用制度化手段固化優(yōu)化后的流程和持續(xù)改善
往往管理層在關(guān)注一個(gè)項(xiàng)目的時(shí)候,項(xiàng)目會(huì)比較順利地推進(jìn),管理層發(fā)生變化不再關(guān)注,項(xiàng)目就會(huì)停滯下來。同樣,項(xiàng)目在完結(jié)一個(gè)階段或幾個(gè)階段后,大家對(duì)項(xiàng)目的關(guān)注程度會(huì)自然降低,不利于該項(xiàng)目穩(wěn)定持續(xù)地開展。項(xiàng)目都有結(jié)束的時(shí)候,工作要長期有效地推進(jìn)下去,需要從項(xiàng)目管理轉(zhuǎn)變到日常化管理。
保持優(yōu)化后流程長期有效地運(yùn)行,這是許多改善項(xiàng)目面臨的一個(gè)難題。人員變更,流程會(huì)隨之發(fā)生變化。因此,項(xiàng)目改善的文件化和制度化在項(xiàng)目結(jié)束時(shí)尤為重要,由于改善涉及信息流與物流的方方面面,涉及管理體系與流程再造,需要整個(gè)項(xiàng)目團(tuán)隊(duì)參與持續(xù)改善。
創(chuàng)新是企業(yè)發(fā)展的不竭源泉與動(dòng)力,企業(yè)需要?jiǎng)?chuàng)新,需要變革,更需要參與創(chuàng)新和變革的員工。對(duì)于整個(gè)項(xiàng)目的成果,分廠進(jìn)行了團(tuán)隊(duì)獎(jiǎng)勵(lì),并對(duì)此進(jìn)行了推廣和宣傳。分廠的技術(shù)創(chuàng)新和管理創(chuàng)新項(xiàng)目參與率也得到了提高,形成了團(tuán)隊(duì)參與改善的企業(yè)文化氛圍。
航空特種設(shè)備制造公司精益六西格瑪管理項(xiàng)目實(shí)施效果
1.創(chuàng)新了部門項(xiàng)目管理策劃方式
通過創(chuàng)新項(xiàng)目管理模式,對(duì)分廠組織機(jī)構(gòu)的調(diào)整,建立組織團(tuán)隊(duì),減少了計(jì)劃與技術(shù)之間的推誘扯皮現(xiàn)象。特別是針對(duì)新品,以工藝技術(shù)人員為龍頭,組建由計(jì)劃、生產(chǎn)操作、專家等人員參與實(shí)施的技術(shù)項(xiàng)目負(fù)責(zé)小組,從項(xiàng)目訂單的任務(wù)接收到產(chǎn)品交付的整個(gè)過程進(jìn)行項(xiàng)目管理,將新品的項(xiàng)目開發(fā)周期由原來的3-4個(gè)月縮短至1-2個(gè)月。
通過項(xiàng)目管理,提升了團(tuán)隊(duì)成員的管理能力,團(tuán)隊(duì)建設(shè)取得成功,從而形成了良好的團(tuán)隊(duì)氛圍和創(chuàng)新、務(wù)實(shí)、高效和奉獻(xiàn)的團(tuán)隊(duì)精神。

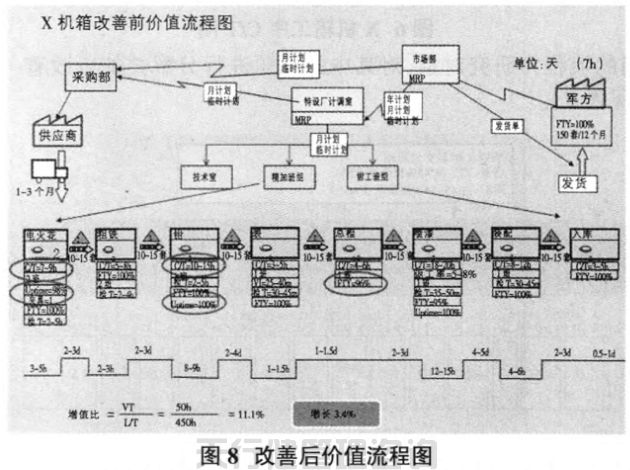
2.項(xiàng)目實(shí)施結(jié)果
改善后,X機(jī)箱產(chǎn)品的價(jià)值流增值比增長3.4%(圖8),瓶頸工序的時(shí)間降低(圖9),接近或低于TT時(shí)間。
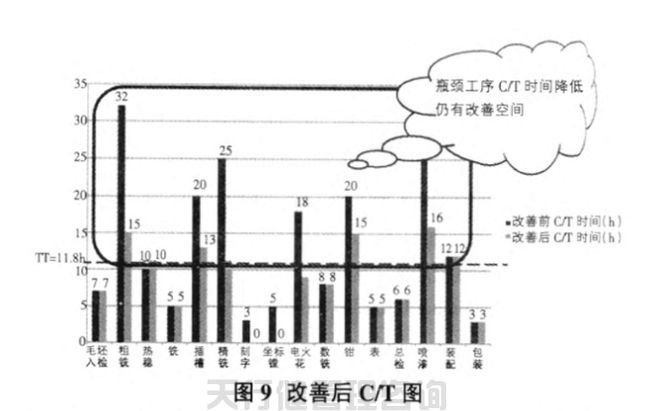
項(xiàng)目改善通過內(nèi)部管理和技術(shù)創(chuàng)新,增加專用工裝,現(xiàn)場6S改善,對(duì)外部資源進(jìn)行培養(yǎng)培育和技術(shù)支持等方法和措施,將產(chǎn)品每批交付周期由改善前的45-84天縮短至30-43天,F(xiàn)TY由改善前的60%提升至96%。雖然交付周期離項(xiàng)目目標(biāo)30-35天有差距,但從時(shí)間序列圖(圖10)上可以看出,目前產(chǎn)品的交付周期比較穩(wěn)定,在目標(biāo)值30-35天內(nèi)波動(dòng),后期還需進(jìn)一步收集項(xiàng)目數(shù)據(jù),進(jìn)行監(jiān)控。
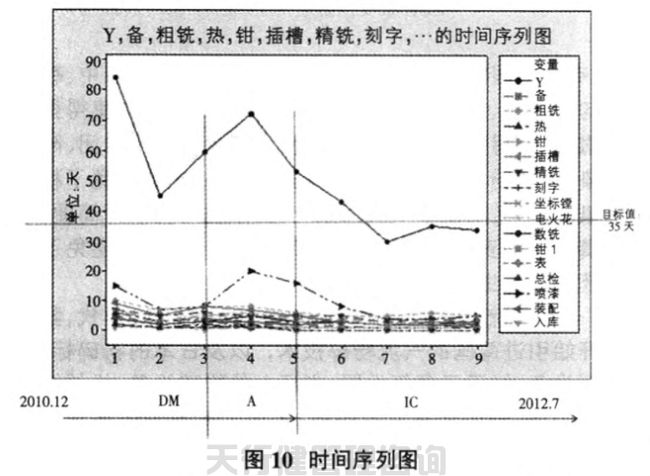
通過流程梳理,得到質(zhì)量、周期與計(jì)劃完成率之間的效應(yīng)關(guān)系(圖11)任何項(xiàng)目的成功,不僅僅是某幾項(xiàng)改善的成功,而是員工不斷參與,充分發(fā)揮各自智慧和力量,由點(diǎn)點(diǎn)滴滴小的改善匯集而成的。雖然改善還需進(jìn)一步,但任何事情沒有最好,只有更好。
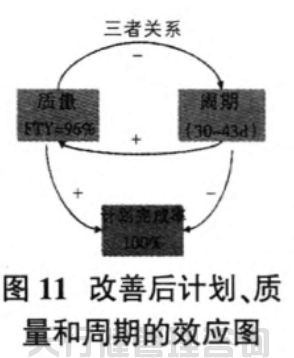
3.項(xiàng)目改善效果
通過對(duì)X機(jī)箱項(xiàng)目的梳理和改善,項(xiàng)目直接財(cái)務(wù)節(jié)余200余萬元。實(shí)施半年多來,共完成機(jī)箱產(chǎn)品80套,滿足了客戶需求。將流程梳理的方法和模式進(jìn)行推廣和應(yīng)用后,整個(gè)機(jī)箱產(chǎn)品的產(chǎn)值同比增長145%。